With the progress of engineering technology, human beings have created various mechanical, electronic, and information systems. However, the structures and functions found in the natural world, especially in living organisms, and the mechanisms of biological activities are still largely unknown and have not yet been reproduced by artificial systems. In recent years, soft materials, such as functional polymers, hydrogels, and bio-derived molecular materials, have attracted much attention, and research on new mechanical, electronic, and information systems that actively utilize molecular reactions is progressing. We are exploring methodologies for microfabrication and microstructure construction using these soft materials, aiming to construct a system that can reproduce natural phenomena and biological mechanisms in an engineering manner (Micro-scale soft robotics).
Soft Spiral-Shaped Microswimmers for Autonomous Swimming Control
"In nature, most microorganisms have motility, which is essential for their survival or reproduction. To move, some microorganisms have evolved soft spiral-shaped flagella, which rotate through specialized motors. Many of these microorganisms can change the morphology of their spiral-shaped flagella to control their motility. Herein, by mimicking these flagella, spiral-shaped microswimmers are developed for various applications, such as target drug delivery, micro-object transport, and micro-fluid manipulation. In previous studies, numerous fabrication methods of spiral-shaped microswimmers are developed. However, the swimming direction and velocity are controlled only by external systems, such as magnetic fields, because the spiral body is not able to deform. Therefore, this soft spiral-shaped microswimmer for autonomous swimming control by detecting surrounding stimuli is proposed. The velocity of microswimmer largely depends on the geometry of the microswimmer’s body. Through usage of a stimuli-responsive hydrogel in the microswimmer, the geometry autonomously changes in response to the surrounding stimuli. Using finite-element simulation, it is revealed that the pattern angle is an important parameter for acceleration/deceleration of the microswimmer. The dimensionless velocity of the fabricated bilayered spiral swimmer changes by deforming the geometry in response to the surrounding thermal stimuli."
[Ref] K. Yoshida et.al., Advanced Intellignet Systems, 2020. [link]
ATP-driven artificial muscle actuator composed of actomyosin-collagen hybrid hydrogel
"We propose an elastomeric microrobot actuated by ATP-driven biological traction of actomyosin. Our robot is composed of a PDMS thin film part as a body and an actomyosin-embedded collagen hydrogel part as a linear motor. The actomyosin drives the hydrogel linear motor by the hydrolysis of ATP. This actomyosin linear motor could repeatably contract by adding ATP and stretching similar to the driving mechanism of our body. By combining the linear motor part and PDMS actuator part, we succeeded in driving the whole device by the traction force of actomyosin. The traction force generated by the linear motor was estimated from the deformation of the PDMS body. We believe that our device would be a new approach to apply biological motor for micro actuators."
[Ref] K. Kohno, et.al., Proceedings of MicroTAS 2021.
Our bodies are composed of various organs and tissues. It is known that the structures of these organs and tissues in vivo are composed of a wide variety of cells arranged three-dimensionally. If we can artificially mimic these in vivo structures in vitro, it will be possible to reconstruct the functions of living organs and tissues. In our group, we aim to establish a bottom-up method to use cells as materials from an engineering viewpoint, and to create ordered three-dimensional tissues, and to express physiological functions in vitro. Our research aims to create artificial tissue models for regenerative medicine and pathological elucidation, and to apply this technology as a tool for new drug development.
Human iPSC-derived microfiber-shaped artificial cardiac tissues
"We propose a core-shell microfiber-shaped cardiac tissue as a drug screening model with a fixation-free contractile force measurement system. The contractile force of the hiPSC-derived cardiac tissue can be calculated only with a motion analysis, thanks to a shell of hydrogel covering the cardiac tissue. Thus, the system can evaluate the behavior of the tissue in drug screenings without any specific equipment. We demonstrated drug screening tests with pharmaceuticals on our microfiber tissues, resulting in 102.7% increase of contractile force with isoproterenol and 56.3% decrease with propranolol. Our cardiac drug screening model can easily reproduce and evaluate cardiac disease models, and would contribute to the pathological research of unexplained cardiac diseases and pharmacokinetic testing."
[Ref] A. Masuda et al., Proceedings of MEMS 2022.
[Related papers]
K. Fukada et al., Biotechnology and Bioengineering, 2022.[link]
Y. Kurashina et al., AIP Bioengineering, 2019.[link]
H. Onoe et al., Nature Materials, 2013.[link]
Vascular embolization of radiopaque hydrogel microfiber using
ultra-minimally invasive technique
"Animal pathology models play an important role in elucidating pathology, evaluating drug efficacy, and studying therapeutics. This paper presents the creation of a rats’ renal failure model by embolizing the renal artery using radiopaque hydrogel microfibers. By using a dual coaxial laminar flow microfluidic device, barium alginate gel microfibers containing zirconia particles were fabricated. Since the zirconia particles are radiopaque, the microfiber can be delivered and embolized while confirming the position of the microfiber in real time under X-ray imaging. The delivery of microfibers through a catheter into the renal artery of rats to create a renal failure model was tested. The radiopaque microfibers were visualized by X-ray imaging when delivered by a catheter. Furthermore, the microfibers remained stable for 2 weeks after delivery. In addition, by adjusting the number of microfibers, two different rat models with severe and mild renal failure conditions were created. The proposed delivery of radiopaque hydrogel microfibers to create an embolization model is expected to be an effective approach to control the degree of symptoms and elucidate the pathology."
[Ref] N. Takakura, et al., Materials & Design, 2022.[link]
Flexibly deformable artificial blood vessels for tharmacokinetic testing models
"Since the biochemical reaction of blood vessels plays an essential role in immune response or various diseases, in vitro vascular models have high demand from medical fields. However, vascular models often tend to be difficult to mimic the biomedical reaction faithfully because of the lack of implementation of the tissue deformation. Here, an inflammatory mediator-induced deformation reaction of a blood vessel on a flexibly deformable collagen hydrogel tube device is reproduced. A self-standing collagen tube enables the tissue to deform flexibly in biochemical reactions and achieves contraction both at the tissue and cell levels. The contraction of tissue relieves the stress between cells under reaction to maintain cellular junctions even tight junctions are broken. Also, the drug perfusion test with antihistamine chemical is easily performed due to the connector part and properly inhibits the inflammatory reaction. Moreover, the traction force on endothelial cells is analyzed as about 0.9 μN on two types of scaffolds with different stiffness. It is believed that the potential of the flexible tissue model to reproduce biochemical reactions can contribute to the fabrication of vascular tissue models mimicking in vivo in high similarity as a platform for biomedical research and pharmacokinetic testing."
[Ref] S. Itai, et.al., Advanced Healthcare Materials, 2022.[link]
[Related papers]
S. Itai et al., Biofabrication, 2019.[link]
ECM-based in vitro vascular models with complex mechanical stimuli
"We present an extracellular matrix (ECM)-based stretchable microfluidic system for culturing in vitro threedimensional
(3D) vascular tissues, which mimics in vivo blood vessels. Human umbilical vein endothelial cells (HUVECs) can be cultured under perfusion and stretch simultaneously with real-time imaging by our proposed system. Our ECM (transglutaminase (TG) cross-linked gelatin)-based microchannel was fabricated by dissolving water-soluble sacrificial polyvinyl alcohol (PVA) molds printed with a 3D printer. Flows in the microchannel were analyzed under perfusion and stretch. We demonstrated simultaneous perfusion and stretch of TG gelatin-based microchannels culturing HUVECs. We suggest that our TG gelatin-based stretchable microfluidic system proves to be a useful tool for understanding the mechanisms of vascular tissue formation and mechanotransduction."
[Ref] A. Shimizu, et.al., Lab on a Chip, 2020.[link], Highlighted in Eurekalart (video) (AAAS)
[Related papers]
A. Shimizu, et al., Biomicrofluidics, 2020.[link]
Three-dimensional artificial intestinal tube with a crypt-like inner surface
"Crypt-like structures are indispensable to fabricating an artificial intestinal tissue reproducing the arrangement of cell types in vivo. This paper presents the fabrication of an artificial intestinal tube with an uneven inner wall created by electrolysis-triggered microbubbles. During the fabrication process of a scaffold, microbubbles were generated on a tungsten electrode to form cavities on the inner surface of the collagen hydrogel tube. The method can fabricate numerous crypt-like structures in the order of a hundred micro-meter quickly. We believe that our device will be a platform for investigating complex intestinal diseases due to its high biomimetic properties."
[Ref] M. Kawahara et.al., Proceedings of MEMS 2022
S. Tanaka, et.al., Proceedings of MicroTAS 2022.
Differentiation of 3D‐shape‐controlled mouse neural stem cell to neural tissues in closed agarose microchambers
"This paper describes three‐dimensional (3D) tissue shape control of mouse neural stem cell (mNSC) micro tissues by using closed agarose microchambers for effective differentiation induction of neurons in vitro. Our agarose microchambers, made by micromolding, can be sealed with an agarose sheet to form the mNSC tissues along the shape of microchambers. We constructed lane‐shaped mNSC tissues with different width (60-210 μm) and thickness (25-95 μm) dimensions and induced differentiation to neurons with differentiation medium. We found that in thick tissues (thickness: >60 μm), distribution of differentiated neurons was not uniform, whereas in thin tissues (thickness: 30 μm), differentiated neurons were uniformly distributed with high differentiation efficiency. Our system to construct in vitro 3D neural tissues having uniformly distributed neurons at high differentiation ratio, could become an effective tool for drug screening using 3D neural tissues and 3D mNSC tissues under differentiation induction."
[Ref] Matsushiro, et.al., Biotechnology and Bioengineering, 2018. [link]
[Related papers]
S. Itai, et al., Biomedical Microdevices, 2020.[link]
Artificial static/dynamic self-assembly systems
Understanding of dynamic and complex self-assembly and self-organization phenomena, which are frequently seen in nature (especially in life system), is one of the centerpiece of science in the past century. These systems are usually hierarchical and dynamic in the range from molecular interactions (nanometer-scale) to micro-to-millimeter structures, and require a non-equilibrium open system for both materials and energy. Aattempts to artificially reconstruct such self-assembly or self-organization systems have recently been focused as one of the ultimate goals for both scientists and engineers. Our group has explored to understand these complex and diverse mechanisms of self-assembly and self-organization, and has challenged the artificial reconstruction of those systems both from the standpoints of science and engineering.
Dynamic transformation of self-assembled structures using anisotropic magnetized hydrogel microparticles
"This paper describes a system through which the self-assembly of anisotropic hydrogel microparticles is achieved, which also enables dynamic transformation of the assembled structures. Using a centrifuge-based microfluidic device, anisotropic hydrogel microparticles encapsulating superparamagnetic materials on one side are fabricated, which respond to a magnetic field. We successfully achieve dynamic assembly using these hydrogel microparticles and realize three different self-assembled structures (single and double pearl chain structures, and close-packed structures), which can be transformed to other structures dynamically via tuning of the precessional magnetic field. We believe that the developed system has potential application as an effective platform for a dynamic cell manipulation and cultivation system, in biomimetic autonomous microrobot organization, and that it can facilitate further understanding of the self-organization and complex systems observed in nature."
[Ref] S. Yoshida, et al., Journal of Applied Physics, 2016. [link]
Microfiber-Shaped Programmable Materials with Stimuli-Responsive Hydrogel
"Programmable materials have artificially designed physical shapes responding to external stimuli, as well as high design capability and high flexibility. Here, we propose a microfiber-shaped programmable material with an axial pattern of stimuli-responsive (SR) and nonresponsive hydrogels. The SR pre-gel solution was mixed to sodium alginate pre-gel solution for instantaneous gelation with ionic crosslinking and solidified on a nonresponsive hydrogel microfiber with a valve-controlled microfluidic system. A design of microfiber-shaped programmable material (patterned position of SR regions) could be flexibly altered by changing a coded sequence program. We confirmed that the three-dimensional (3D) coil-like structures were self-folded at the patterned SR regions responding to the thermal stimulus and that the chirality of the self-folded 3D coil-like structures depends on the condition of the stimulus to the microfiber. Finally, interaction with objects using the programmable microfiber as a soft actuator was demonstrated. Our microfiber-shaped programmable materials expand possibilities of fiber-based materials in biomimetics and soft robotics fields
."
[Ref] N. Takeuchi, et al., Soft Robotics, 2022. [link]
Sensing devices for biological and environmental information by integrating functional materials
Research on functional materials is remarkable, and new materials are being created every day. We believe that micro-scale processing technology and MEMS (Micro-Electro-Mechanical Systems) are powerful tools to integrate these materials and create devices that we can use in our daily life. We propose new devices by developing methodologies to integrate colloidal crystals, nanocarbon materials, spontaneously degradable polymeric materials, and functional biomolecular materials to function as a single system.
Graphene-based wireless tube-shaped pressure sensor for in vivo blood pressure monitoring
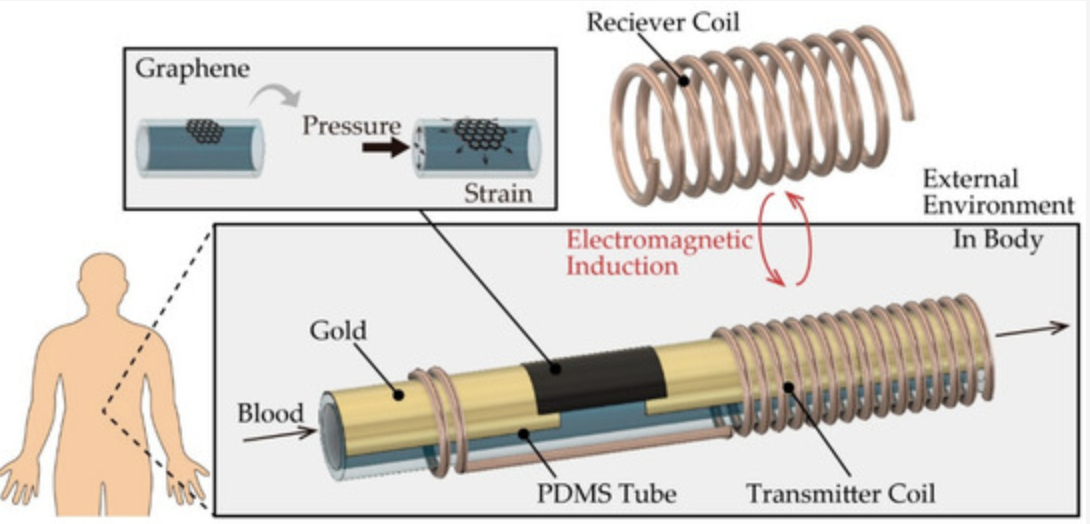
"We propose a wireless pressure sensor composed of a graphene sheet and a transmitter coil integrated with a polydimethylsiloxane (PDMS) tube. The pressure inside the tube was monitored wirelessly using an external receiver coil. We then monitored the typical blood pressure range, 12−20 kPa, using this fabricated sensor by changing the turn number of the receiver coil and the overlapping length of the coils. Furthermore, we demonstrated wireless blood pressure measurement by connecting our sensor to the blood vessel of a rat. Our results suggested that this sensor can be easily inserted between an implantable medical device and blood vessels for in vivo blood pressure monitoring. The proposed wireless pressure sensor could also be suitable for monitoring in vivo implanted medical systems, such as artificial organs and pump systems."
[Ref] N. Inoue, et al., Micromachines , 2019. [link]
N. Inoue, et al., Journal of Micromechanics and Microengineering, 2018. [link]
Edible wireless sensor for gut bacterial monitoring
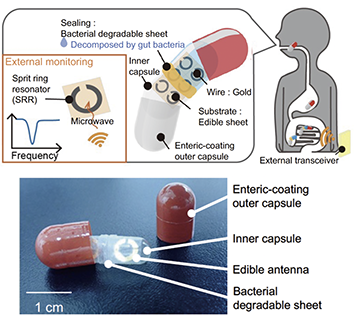
"This report describes an ingestible capsule sensor that can wirelessly detect the activity of gut bacteria by irradiating microwaves from outside the body. The proposed sensor is composed of only edible materials: the critical sensing material is a film made of dietary fiber that is decomposed by gut bacteria. We confirmed that the dietary-fiber-made film can be decomposed by gut bacteria, bifidobacteria. For wireless communication, we fabricated an ingestible antenna made from rice paper and gold with a split-ring resonator (SRR), one of the elements of electromagnetic metamaterials. Our sensor fulfills swallowable size and wireless communication requirements for the first time and would be a safety sensor for gastrointestinal (GI) tract monitoring. We believe that our ingestible sensor could be an effective tool for non-invasive biological substances monitoring without retention risk"
[Ref] A. Inami, et al., Proceedings of MEMS 2022.
Fully-degradable wireless soil pH sensor in outdoor environment
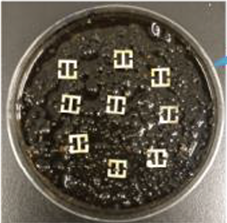
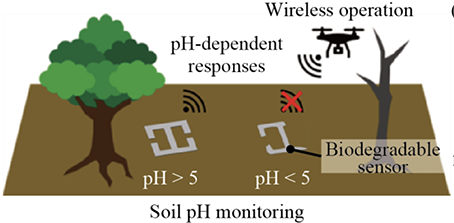
"We propose a wireless and battery-free soil pH sensor made entirely of degradable materials for soil pH monitoring in outdoor environments. The sensor consists of magnesium (Mg) electric antenna based on inductor-capacitor circuit resonance with hydroxyapatite (Ca10(PO4)6(OH)2, HA) coating, enabling degradation of the sensor in acid soil conditions. In this report, we succeeded in measuring the changes over time of different electromagnetic responses in soils with different soil pH. Furthermore, the electromagnetic response of the sensor was also demonstrated in the outdoor field experiment. We believe that our biodegradable soil pH sensor could apply to low-cost, in situ, and environmentally friendly monitoring of soil pH."
[Ref] K. Hori, et al., Proceedings of Transducers 2021.
K. Sakabe, et al., Proceedings of MicroTAS 2022.
Eye-recognizable structural-color biochemical hydrogel sensors for healthcare and environmental monitoring
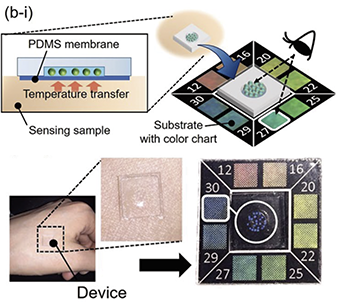
"This paper presents eye-recognizable and repeatable biochemical flexible sensors using low angledependent stimuli-responsive photonic colloidal crystal hydrogel (PCCG) microbeads. Thanks to the stimuli-responsive PCCG microbeads exhibiting structural color, users can obtain sensing information without depending on the viewing angle and the mechanical deformation of the flexible sensor. Temperature-responsive PCCG microbeads and ethanol-responsive PCCG microbeads were fabricated from a pre-gel solution of N-isopropylacrylamide (NIPAM) and N-methylolacrylamide (NMAM) by using a centrifuge-based droplet shooting device (CDSD). As a proof-of-concept of thin and flexible biochemical sensors, temperature- and ethanol-sensing devices were demonstrated. By comparing the structural color of the stimuli-responsive PCCG microbeads and the color chart of the device, sensing information, including skin temperature of the human body and ethanol concentration in alcoholic beverages, was obtained successively. We expect that our device design using low angle-dependent stimuli-responsive PCCG microbeads would contribute to the development of user-friendly biochemical sensor devices for monitoring environmental and healthcare targets."
[Ref] M. Tsuchiya, et al., Scientific Reports, 2019. [link]
Mechanically-sensitivity-tunable structural-color biochemical hydrogel sensor
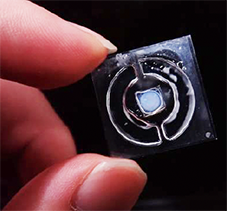
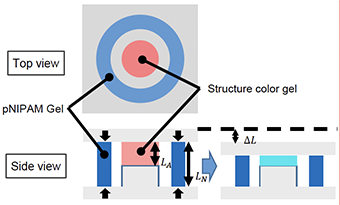
"This paper describes an eye-recognizable structural-color hydrogel chemical sensor that can mechanically adjust its sensitivity. In our system, the Ag+-ion-responsive DNA-aptamer hydrogel and structural-color hydrogel are patterned between two substrates. We built the working theory of our sensor based on mechanics of material and plotted the sensitivity characteristics with respect to its design parameters: the geometric designs and the Young’s moduli of the hydrogels. To examine this theory, we fabricated the sensor device and its sensitivity to Ag+ ions showed good agreement with the theoretical calculation derived from material of mechanics ."
[Ref] R. Yamawaki, et al., Proceedings of MEMS 2022.
R. Ueno, et al., Proceedings of MicroTAS 2022.
Oil-sealed hydrogel microwell array for single-cell-level exosome analysis
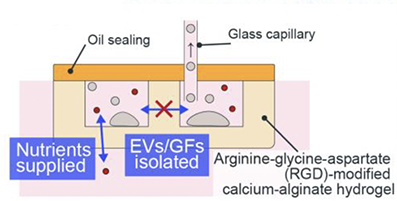
"We proposed an oil-sealed hydrogel microwell array for analysis of secretory components from isolated single cells. The purpose of our device is to realize the isolation of the secretory components during cell culture by combining the semi-permeable arginine-glycine-aspartate (RGD)-modified calcium alginate microwell and the oil sealing. We demonstrated the oil-sealing property, the impermeability to extracellular vesicles (EVs) or growth factor proteins (GFs), and the permeability to nutrients of our device by using three types of fluorescent particles with different diameters. We believe that our oil-sealed hydrogel microwell array will contribute to biomedical analysis on single-cell metabolism that helps to understand the mechanisms of various diseases."
[Ref] C. Yamagata, et al., Proceedings of microTAS 2022.
Hierarchical microsystems with DNA nanotechnology
In this half century, sientists found DNA playing a central role in coding, replicating and transcripting genetic information in life system. As well as advances in the biological sence, DNA molecule itself has resently been used as functional nanoscale building blocks to engineer nanoscale structures, molecular calculation and computing, chemical sensing and structure conformation (actuation), recognized as DNA Nanotechnology. Our group has focused on the use of DNA molecules as a programmable linker between molecular objects and micro-scale objects, and has studied on constructing macroscopic structures and systems controlled by molecular events.
DNA-programmed micropatterning of living cells
"Synthetic DNA strands can be attached to the plasma membrane of living cells to equip them with artificial adhesion “receptors” that bind to complementary strands extending from material surfaces. This approach is compatible with a wide range of cell types, offers excellent capture efficiency, and can potentially be used to create complex multicellular arrangements through the use of multiple capture sequences.The utility of this approach is demonstrated through the observation of patterned cells as they communicate by diffusion-based paracrine signaling."
[Ref] H. Onoe, et al., Langmuir, 2012. [link]
Repeatable detection of Ag+ ions using a DNA aptamer‐linked hydrogel biochemical sensor
"This paper describes repeatable detection of Ag+ ions using a DNA aptamer-linked hydrogel biochemical sensor integrated with a microfluidic heating system. Biochemical sensors that respond to chemical compounds and produce detectable signals have a critical role in many aspects of modern society. In particular, the repeatable measurement of environmental information such as toxic substances including Ag+ ions could be expected to improve the environment. The DNA aptamer is an attractive candidate because of the stability and the selectivity of binding to chemicals. However, previous DNA aptamer biochemical sensors could not measure repeatedly because those sensors did not have initializing functions. To overcome this challenge, we proposed a DNA aptamer-linked hydrogel biochemical sensor integrated with the microfluidic heating system enabling repeatable detection of Ag+ ions. The binding Ag+ ions are dissociated by heating and flushing through the integrated microfluidic heating device. The DNA aptamer-linked hydrogel had the capability to detect a wide range of Ag+ ion concentrations including a toxic range for various aquatic organisms. Finally, we demonstrated the repeatable detection of the Ag+ ions. These results indicated that our proposed biochemical sensor is expected to use for long-term monitoring with high stability in ambient temperature and low power consumption.."
[Ref] K. Yoshida, et al., Scientific Reports, 2022. [link]
Functional hydrogel microbeads formation technology and drug delivery (DDS) applications
In general, when structures are reduced to the micro- and nanoscale, the ratio of surface area to volume increases due to the scaling effect. This allows physical properties different from those of materials we perceive in our daily lives to dominate, and can bring out new material possibilities. In this laboratory, we are studying the formation of microgel beads using various functional hydrogel materials by utilizing "centrifugal-driven microfluidic device technology," which enables the easy formation of micro-scale beads. The formed microgel beads are also used for medical applications, mainly in drug delivery systems (DDS).
Phase-separated hydrogel microbeads from a homogeneous mixture of multiple polymers
"This paper reports a unique phase separation behavior, a simultaneous-crosslinking-driven phase sep- aration in co-gelation (SPSiC) core−shell microgel that spontaneously forms from a homogeneous pre- gel solution of multiple polymers. The SPSiC microgel, composed of an alginate shell and an N - isopropylacrylamide (NIPAM) core, were synthesized by a single fabrication step wherein a mixed pre-gel solution of sodium alginate and NIPAM monomer was ejected by centrifugation with photo- polymerization and ion crosslinking instantaneously. Phase separation was modeled by varying the degree of polymerization and the size of the polymer chain. Moreover, an implantable, multi-functional drug de- livery system combined with a transdermal glucose sensor was demonstrated with core−shell Janus SPSiC microgels. This work shows a macroscopic phase separation behavior, which occurs during the gelation process, and also provides a simple and unique methodology to create multifunctional bio-microprobes."
[Ref] Y. Kurashina, et al., Applied Materials Today, 2021. [link]
Ultrasound-triggered on-demand drug delivery using hydrogel microbeads
"Ultrasound-triggered drug delivery has been widely researched for its potential to improve the therapeutic efficacy of drugs. This paper presents drug release using hydrogel microbeads with release enhancer for efficient ultrasound-triggered drug delivery. By using a centrifuge-based microfluidic device, drug-model-encapsulating calcium alginate hydrogel microbeads containing tungsten particles with high acoustic impedance were fabricated. Because the tungsten particles work as release enhancer, the hydrogel microbeads become to have high sensitivity to ultrasound with localized variation in acoustic impedance so that the release rate of drug models improves. By applying ultrasound at 20 kHz to the hydrogel microbeads, the release of fluorescent silica nanoparticles that are a drug model for virus vectors, micelles, and proteinswas tested. Importantly, the proposed hydrogel microbeads released the drug model even under a cavitation-suppressed environment. Furthermore, the additional coating on the hydrogel microbeads with poly-L-lysine enabled us to adjust the release rate of the drug model. The proposed ultrasound-triggered drug release system using release enhancer is expected to be an effective approach for expanding the varieties of applicable treatments using on-demand drug delivery systems."
[Ref] T. Kubota, et al., Materials & Design, 2021. [link]
Janus Hydrogel Microbeads for Glucose Sensing with pH Calibration
"We present fluorescent Janus hydrogel microbeads for continuous glucose sensing with pH calibration. The Janus hydrogel microbeads, that consist of fluorescent glucose and pH sensors, were fabricated with a UV-assisted centrifugal microfluidic device. The microbead can calibrate the pH values of its surroundings and enables accurate measurements of glucose within various pH conditions. As a proof of concept, we succeeded in obtaining the accurate value of glucose concentration in a body-fluid-like sample solution. We believe that our fluorescent microbeads, with pH calibration capability, could be applied to fully implantable sensors for continuous glucose monitoring.."
[Ref] M. Ando, et al., Sensors, 2021. [link]
MEMS/NEMS/microfluidics
Top-down machining processing at micro- and nano-scale have been deepned with various state-of-art technologies. Among these technologies, the MEMS (Micro-Electro-Mechancal Systems) technology based on photolithograpy and semiconductor processing has improved the accuracy of the fabrication and has expand their target materials for this decades. Our group has developed MEMS/NEMS/microfluidic systems that could combine multiscale elements from molecular to device scales and has also focuesd on device phyisics through the fabrication.
Liquid-filled flexible micro suction-controller array for enhanced robotic object manipulation
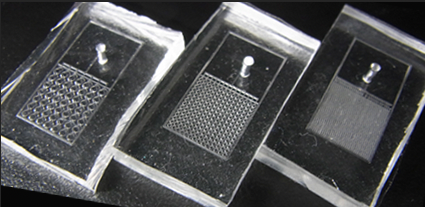
"With the intent to enhance robotic manipulation, this paper describes a novel liquid-filled flexible micro suction-controller array (MISCA) for humanoid robotic hands that can hold curved or grooved surface objects. The proposed MISCA comprises 49 suction units arrayed in a 10 mm × 10 mm area of flexible polydimethylsiloxane sheet. Each 1 mm diameter suction unit generates suction force independently. An incompressible working fluid (ethylene glycol) is injected or drained through microchannels in the MISCA using a syringe pump to control the suction force. In experiments, the proposed MISCA effectively generated suction forces of 0.96-1.54 N on flat surfaces, 0.43-0.63 N on cylindrical surfaces, and 0.60-0.83 N on spherical surfaces. In addition, the proposed MISCA was demonstrated to successfully manipulate a 75 g flat object (a watch), a 1-g grooved object (a yen coin), and a curved object (a tablet) using suction control."
[Ref] Nishita et al., Journal of Microelectromechanical Systems, 2017. [link]
Shape-recognizable Origami sheet device with single walled carbon nanotube strain sensor
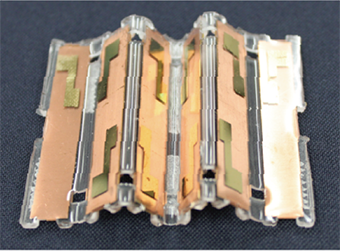
"This article describes a shape-recognizable sheet device using origami structures with single-walled carbon nanotubes (SWCNTs) strain sensors. Recently, a sheet-like measurement system that is directly attached to an object has been attracting attention for obtaining the shape, motion, and deformation of the object as alternative systems with external cameras. However, previous sheet-like measurement systems are difficult to distinguish between the stretch and the bend of the object appropriately. Here we propose a sheet-like measurement system that can distinguish the stretch and the bend individually by using origami structures. We formed a strain sensor using SWCNTs that was deposited on a substrate to form a 5-7 nm thin film. By patterning the SWCNTs strain sensors, origami-based sheet devices were fabricated. We confirmed that our origami sheet device obtained the bending and stretching information separately by attaching the device to cylinders. We believe that the origami system could contribute to the observation of complex deformations such as artificial skin, human interface, and biomedical applications."
[Ref] T. Mori, et al., Journal of Microelectromechanical Systems, 2021. [link]
Microfluidic-based flexible reflective multicolor display
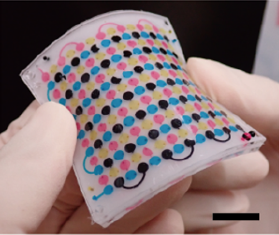
"This paper describes a microfluidic-based flexible reflective display constructed using dyed water droplets and air gaps as pixel elements. Our display is composed of a flexible polydimethylsiloxane sheet with a connected pixel-patterned microchannel. Several types of dyed water droplets and air gaps are sequentially introduced to the microchannel through a suction process to display a multicolor image. The displayed image is stable and can be retained without an energy supply. To ensure that images are displayed correctly, the geometric parameters of the dot pixel design and minimum differential pressure necessary to drive the water droplets are evaluated. As a demonstration, we successfully display three-color dot-matrix reflective images and bitmap characters in the microchannel. Our proposed method can be applied to energy-less and color-changeable displays for use in future daily-life accessories, such as bags, shoes, and clothes, and can change the surface color and pattern of these accessories."
[Ref] J. Muramatsu, et al., Journal of Micromechanics and Microengineering, 2021.[link]
K. Kobayashi, et al., Microsystems & Nanoengineeringvolume, 2018. [link]